Food quality control is fundamental to ensuring food safety. What software is traditionally used in the food industry, such as ERP, LIMS, and ELN? How can the CIKLab application help you specifically manage surveillance plans and all food safety analyses?
Sommaire :
1) What is food quality control ?
2) What are the different software solutions for food quality control ?
3) What is the Easiest Software for Food Quality Control ?
What is food quality control ?
In general, quality control is a set of operations that involve verifying through measurements that a product meets predefined specifications and determining the compliance with these specifications.
In the food industry, quality control has several objectives:
- Ensuring food safety: Guaranteeing that products are safe for consumption.
- Ensuring regulatory compliance: Making sure that products meet current standards and regulations.
- Maintaining consumer satisfaction: Providing consistently high-quality products that meet consumer specifications and expectations.
- Improving operational efficiency: Quickly identifying issues in manufacturing processes and enabling corrective and/or preventive actions.
To verify established specifications, quality control services use various tests at different stages such as the receipt of raw materials, manufacturing, packaging, etc.
We therefore find two types of quality control:
1- In-line quality control:
This step involves performing a series of quick tests on the production line, focusing both on the intrinsic characteristics of the food product, such as appearance, moisture, viscosity, sugar content, etc., and on aspects related to its market readiness, such as weight verification, label type, and packaging durability. Some tests are automated using sensors, while others are conducted by trained operators directly on the line.
All these controls ensure that the manufacturing process produces products that meet the required criteria.
2- Quality control on the food product itself:
Quality control on the product itself involves, at various stages, more complex analyses that cannot be performed on the production line but require internal and external laboratories.
These analyses include:
- Food safety testing : These tests and analyses verify the absence or compliance with thresholds of certain hazards for consumers, such as microbiological analyses, and tests for chemical and/or biological contaminants.
- Physico-chemical analyses: These involve checking organoleptic criteria (flavor, appearance, odor) and technical parameters (viscosity, pH, moisture).
- Nutritional analyses: These ensure the accuracy of nutrient content claims and verify the presence or absence of certain allergens, where applicable.
These analyses are often conducted in specialized laboratories, which can be internal to the company or outsourced to external laboratories.
In the food industry, quality control is inseparable from food safety testing and thus from outsourcing to third-party laboratories !
The Importance of Control Plans in the Food Industry
In the food industry, all tests and analyses to be performed are organized into a structured set known as a self-control plan, a surveillance plan, or a quality control plan.
Control plans determine:
- The analysis or test to be conducted
- The method
- The acceptance criteria (specifications)
- Who will perform the control (operator, internal laboratory, outsourced laboratories)
- The frequency at which the analysis or test should be conducted
- The measures to be taken in case of a deviating or non-compliant result
Control plans depend on various factors such as hazard analysis, risk assessment, and the process itself. They cover the product at different stages, as well as the manufacturing environment, cleaning controls, CCPs (Critical Control Points), packaging, etc.
The biggest challenge of quality control lies in organizing a multitude of surveillance and analysis plans, each with its own specifications, acceptance criteria, and, most importantly, periodic frequencies
Periodic surveillance plans primarily focus on the analysis of food contaminants, which are outsourced to specialized laboratories.
What are the different software solutions for food quality control ?
The ultimate global solution: ERP (Enterprise Resource Planning)
ERP systems are among the most complex and comprehensive IT solutions in the industry. They connect and coordinate many functions and processes within a company, such as finance, human resources, production, and logistics. ERPs are central and essential for efficiently managing the entire industrial manufacturing flow: from purchasing raw materials to distribution, including production. ERPs integrate inventory management, traceability, billing, and accounting.
Regarding Quality Control:
There are various ERP modules and types tailored to specific sectors, but in the food industry, they are central for managing production recipes, traceability, and inventory (quarantine, rejections, release). Most are suitable for systematic in-line quality control, meaning an inspection plan can be designed and configured for each recipe type. Unfortunately, they quickly become limiting for managing surveillance analyses, outsourcing to independent laboratories, generating technical documentation (CoA, technical sheets), and utilizing analytical data. This often forces quality control departments to continue managing outsourcing and periodic analyses on other types of platforms.
Advantages:
- Comprehensive view of the company
- Integration of several essential management functions, especially traceability and inventory status (quarantine, release, etc.) for recalls and withdrawals.
Limitations:
- Very high cost and implementation can take years.
- It is a strategic and global project for the company, and it's not uncommon that by the end of an ERP implementation project, quality control management is reduced to the bare essentials.
💡 Key Insights :
Due to their structure, ERPs can lack flexibility, intuitiveness, or even specific modules to easily manage periodic surveillance plans, outsourcing, integration of external results, and detailed and specific data analysis.
Laboratory-specific solution: LIMS (Laboratory Information Management System)
LIMS is designed to optimize laboratory operations by automating processes specifically related to the management of samples to be analyzed. It allocates the necessary resources for conducting analyses, including human, material, consumable, technical, and financial resources. LIMS are extremely powerful solutions truly dedicated to large industrial structures that internalize a significant number of analyses. In essence, LIMS are the ERPs of analytical service laboratories.
Advantages
- Data Centralization: Centralizes data for easy access and sharing within the laboratory.
- Powerful Traceability Management: Enhances traceability of samples, analyses, and reports.
- Laboratory-Specific Design: Specifically designed for analytical laboratories.
Limitations :
- High Cost: Initial investment and maintenance costs are often high.
- Long Implementation and Setup: Implementing and configuring a LIMS can be time-consuming and complex.
- Challenges in Managing External Analyses: Difficulty in handling external analyses, planning by product type, and control frequencies.
💡 Key Insights :
LIMS are perfectly suited for managing internal analyses. However, very few LIMS manage catalogs of external analyses and subcontracting. Additionally, their focus on sample management limits the ability to work on more comprehensive management of control plans and quality control that do not specifically involve analyses (such as organoleptic tests, CCP verifications, etc.).
The “product-centric” solution: PLM (Product Lifecycle Management)
PLM (Product Lifecycle Management) manages all stages of a product's lifecycle, from design to commercialization. It centralizes product information and facilitates collaboration and communication between various departments such as R&D, production, and marketing. PLM is based on the major pillars of a product's life: Design - Development - Manufacturing - Use - End of Life.
In the food industry, PLM systems manage recipes, technical information including supplier details, nutritional data, and integrate costs. PLM enables faster market launches of new products by finely managing costs and documentation (packaging, labels).
By centralizing and streamlining processes, PLM allows for improved efficiency and quicker response times, ensuring that products are developed, produced, and brought to market effectively and efficiently.
The solution for real-time control: MES (Manufacturing Execution System) / SPC (Statistical Process Control)
The primary goal of an MES is to ensure production efficiency and quality by providing precise and instant visibility into all factory operations. It allows tracking of performance, partial quality control, cost reduction, and production optimization.
Advantages
- Centralization of Shop Floor Controls: Aggregates various controls and checks conducted on the production floor.
- Real-Time Data: Provides up-to-date information on production processes.
- Powerful Control Statistics Management: Enables robust analysis of production data.
Limitations
- Moderate to High Cost: Implementation and maintenance can be expensive.
- Long Setup Time: Configuration and integration require significant time and effort.
- Limited Scope: Primarily focused on production, not covering detailed quality control analytics.
- No Subcontracting Management: Lacks features for managing outsourced processes.
💡 Key Insights :
In the food industry, quality control often involves complex analyses that are frequently outsourced. Consequently, the MES can mainly focus on process monitoring, as it cannot fully address the intricate and subcontracted aspects of quality control.
The solution for managing R&D projects: ELN (Electronic Laboratory Notebook)
Electronic Laboratory Notebooks (ELN) are digital replacements for traditional paper lab notebooks. They are ideal for documenting experiments and results of various types (graphs, chromatograms, sequencing, etc.). Primarily used by R&D departments, ELNs may lack advanced features for comprehensive quality control planning and routine analytical tasks.
Advantages
- Moderate Cost: More affordable than many other laboratory management solutions.
- Digitalization of Lab Notebooks: Replaces paper notebooks with digital versions, making documentation easier and more efficient.
- Effective Documentation: Facilitates the recording of experiments and results.
Limitations
- Lack of Advanced Features: May not support comprehensive management of quality control plans, schedules, outsourced analytics, and routine quality control analyses.
💡 Key Insights :
While ELNs are excellent for documenting R&D activities, they may fall short in providing the necessary tools for overall quality control management and routine analytical operations.
The most used solution: MS Excel!
For decades, Microsoft Excel has been the go-to tool for many companies to manage data, including control plans. Its flexibility, ease of use, and ability to create tables and charts make it a popular choice. However, Excel has limitations when it comes to managing large-scale control plans. File size can become an issue, as can traceability difficulties, data security, and integrity. Real-time collaboration and version management can be problematic. Often, complex macros need to be developed because there is consistently a missing "dimension" to make it an automated and functional solution.
Advantages: Very low cost, flexibility, ease of use, ability to create tables and charts.
Limitations: Handling large volumes of data, necessity to develop complex macros to automate tasks, audit trail issues, data security problems, collaboration difficulties, remote accessibility issues.
Even if Excel is an excellent tool for starting to structure control plans, the accumulation of data quickly calls for more solid, specialized and automatic solutions!
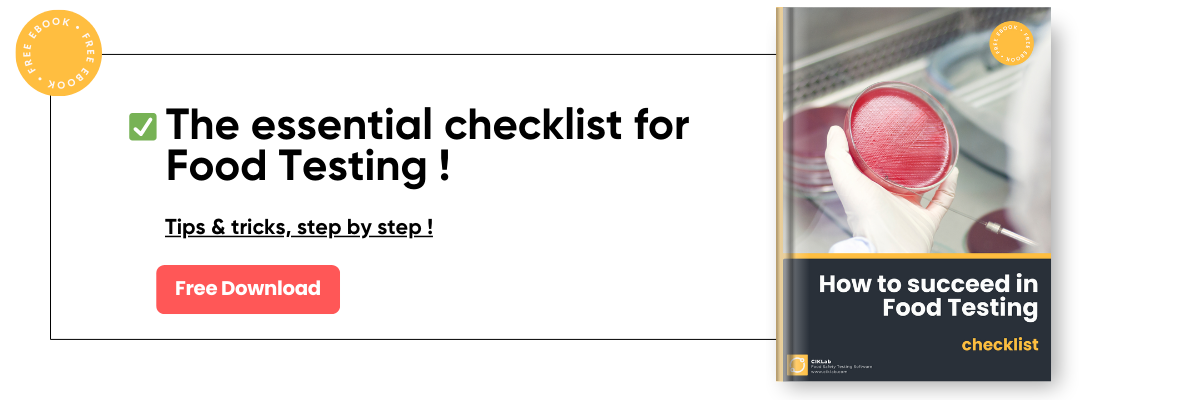
What is the Easiest Software for Food Quality Control ?
CIKLab: The simple and pragmatic application for Food Surveillance Plans
CIKLab is a straightforward, pragmatic application dedicated to food surveillance plans. Accessible online without the need for installation, it simplifies and streamlines the monitoring process for food safety.
CIKLab helps food industry companies rigorously monitor and control critical limits for each identified hazard. With simple and robust test and control settings, the application enables efficient and automatic management of product surveillance plans.
Unlike other software, CIKLab is uniquely configured to handle:
- Control and surveillance plans
- Management and monitoring of analyses and tests
- Outsourced laboratories
- Alerts on periodic analyses
- Exploitation of results
This specialized configuration makes CIKLab the ideal choice for comprehensive and efficient food safety management.
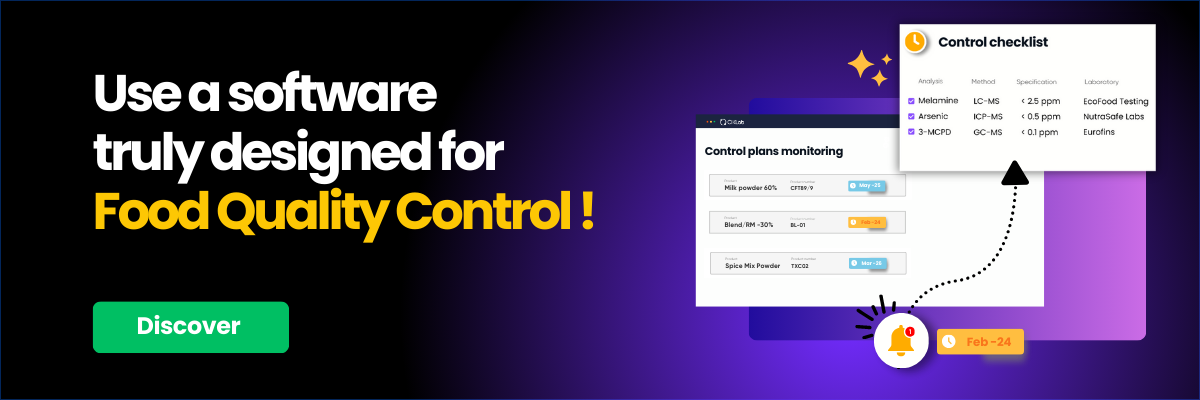
CIKLab ensures precise and reliable management of control plans and analyses, essential for guaranteeing the quality and safety of food products.
Unlike more traditional solutions like ERP systems, which can be rigid and costly, or generic tools like Excel, which have limitations in terms of security and large-scale data management, CIKLab offers a solution specifically tailored to the needs of quality control managers. With an API system, CIKLab can connect and communicate with other software solutions, including ERP systems.
Why not start with software dedicated to control plans?