Sommaire
1) What is a quality control plan?
2) What's the difference between a control plan and a monitoring plan?
3) How to build a solid control plan in 7 steps ?
3) Which software should be chosen to manage analytical control plans?
4) Automate Your Analytical Control Plans with CIKLab.
What is a quality control plan?
An analytical control plan (or self-monitoring plan) is a structured set of analyses and checks, combined with methods, frequency specifications, and sampling. Its purpose is to plan and assess the quality and safety of food products. It's an essential tool for companies in the food industry!It concerns :
- Inputs: raw materials, technological auxiliaries, additives, water, etc.,
- The process (CCP)
- The "work-in-progress" products, intermediate products, and of course, the marketed finished products.
- The manufacturing environment, hygiene, CIP (Clean-in-Place), controlled areas, etc.
👉Download our MS Excel automatic Quality Control Plan !
What's the difference between a control plan and a monitoring plan ?
Some quality control services in industry differentiate between control plans and monitoring plans, making the following distinction :
- A control plan describes what must be checked "systematically" internally and externally on a production batch.
- A monitoring plan involves "periodic checks" of certain parameters, set either randomly or strategically, such as the geographical origin of a product, the purchase volume, the supplier's rating, vulnerability to fraud, etc. The parameters in question are often very costly and/or time-consuming analyses.
Regulatory context
Brief review of the obligations imposed on operators:
"Food business operators and animal feed sector operators shall, at all stages of production, processing, and distribution in the businesses under their control, ensure that food or feed meets the requirements of food law relevant to their activities and shall verify that such requirements are met."
(EC) No 178/2002 Article 18.
"A testing schedule for products should be in place. This may include microbiological, chemical, physical, and organoleptic tests depending on the risks. The methods, frequency, and specified limits must be documented."
BRC 9 - [5.6.1.1]
"Analytical monitoring is a requirement [...] that contributes to food safety."
French - Direction générale de l'Alimentation- Technical instruction DGAL/MUS/2023-11.
How to build a solid control plan in 7 steps ?
The old quality maxim from the 90s, "Write what you do, and do what you write," is definitively outdated! It has since been replaced by a more agile, intelligent, and holistic approach to continuous improvement and "Food Safety Culture."
Yet, unfortunately, constructing a control plan is a complex task, and the first challenge in building a control plan lies precisely in the rigorous planning of what one aims to achieve and in the realization of what has been planned. It's essential that the assessment allows for the continuous improvement of control plans.
For Quality managers in the food industry, implementing a structured control plan is a challenge in itself, as this plan needs to be thought out, established, followed, and constantly improved and modified.
Step 1: The Regulatory Environment: What's the context ?
All the regulatory texts applicable to your sector and product types are a fundamental prerequisite to understand the minimum requirements for your products. This regulatory study is a necessary step to build upon; it's the foundation of your entire quality control system.
Regulations, but also criteria set by professional unions and your clients, can apply to:
- All your products
- Some products
- Certain product categories.
Step 2: What to control and what are the criteria?
On one hand, there are analyses that ensure the quality of your products in terms of nutritional, technical specifications, etc., and on the other hand, there are all the analyses that demonstrate food safety. This will be done in two steps:
- The regulatory study and product prerequisites provide a comprehensive list of what needs to be done and the expected specifications, such as Regulation (EC) 915/2023 for contaminants and Regulation (EC) 2073/2005 for microbiology.
- Regulatory monitoring and reviews are absolutely necessary, just like consulting RASFF alerts or EFSA information.
- The hazard assessment will allow the selection of analyses related to microbiology, chemistry, physics, or allergens.
- Then it's the risk assessment, which depends on the process, suppliers, variability of materials, and their origins that will prioritize the analyses based on a criticality score.
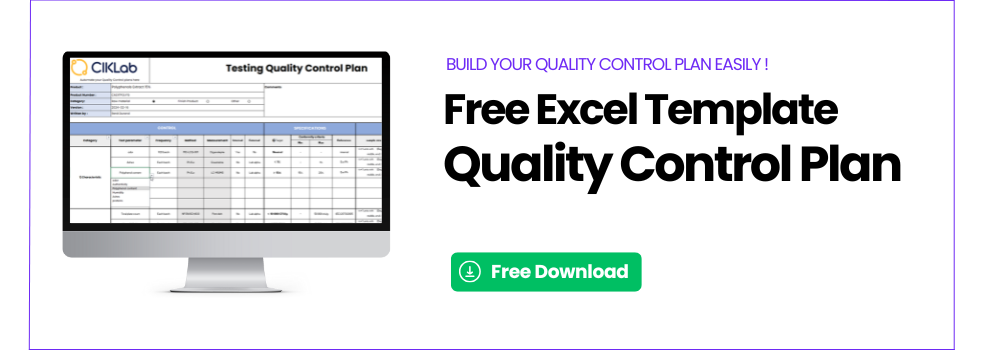
Step 3: Rigorous selection of analyses, it's imperative.
Based on the identified hazards and risks (a combination of the severity of the hazard and its occurrence), it's crucial to select the most relevant analyses. Whether you conduct the analyses internally or outsource them, choose tests that meet the expected specifications based on:
- Performance criteria (sensitivity, recovery, LoD, LoQ, accuracy, uncertainty, reproducibility, etc.)
- The nature of the sample to be tested.
💡 It's recommended to preferably use validated and standardized analyses when available (NF, EN, ISO, Pharmacopoeias) as this facilitates interpretation, comparison of results, and promotes collaboration between the various parties involved.
Step 4: Choose Reliable Laboratories.
Collaborating with independent, specialized, and recognized laboratories is essential to ensure the reliability and accuracy of analysis results. Laboratory accreditation according to the ISO 17025 standard can be a primary selection criterion in some cases (this is not a requirement for self-checks). Fortunately, it's possible to work with non-accredited laboratories, but in this scenario, you will need to demonstrate with the lab that the analysis results are reliable (inter-laboratory tests, audits, comparisons, and monitoring).
Step 5: Define Control Frequencies.
This is obviously the step that poses the most challenges.
Working on control frequencies or periodicities is about finding the perfect balance between safety and efficiency!
The frequency at which analyses are carried out can directly influence the detection of anomalies and, consequently, product safety. Too infrequent analyses can miss non-conformities, while too frequent ones can generate unnecessary costs and tie up resources. Factors determining the frequency of analyses are: Risk assessment, the nature of the product, its vulnerability to fraud, the history of analyses and non-conformities, regulatory (sanitary) requirements, production volume, and costs associated with control analyses.
It would be challenging to give general cases, but after phases of study and mastery Supplier-Product-Process, in the ingredient field for instance, it's not uncommon to find 4 types of frequencies:
-
- Systematic (controls on each batch) e.g.: microbiology, protein content.
- Periodic by lots (1/5 lots) e.g.: mineral content.
- "Temporal" periodicities (1/year, 2/year) e.g.: certain contaminants like melamine.
- Occasional, random, unexpected (1 time) e.g.: Detection of nanomaterials, ionization, during the validation of a product-supplier pairing, for example.
Step 6: Develop Detailed Sampling Plans.
It's about determining the number of samples to be taken, their size, and the sampling frequency. The sampling plan is crucial in many ways since it's the initial stage of an analysis!
- Sampling should be done correctly to avoid "contaminating" the collection (e.g., in microbiology).
- It must represent the batch in question, so be cautious with certain contaminations that can be heterogeneous (e.g., mycotoxins, microbiology).
- The sample size must be substantial and tailored to the analyses being conducted: the risk of not detecting a contaminant increases when the sample size is small, or when the analyte specification is close to the analysis's detection limit.
💡 Regulation (EC) 333/2007 specifies the sampling rules to be followed for self-checks.
Step 7: Monitor and Improve Based on Control Results
The final step involves recording and tracking the analysis results to assess trends and adjust the control plan. This can either mean tightening controls during certain periods (e.g., health alerts) or, conversely, loosening controls on specific parameters when you deem the risks to be managed or statistically controlled.
Which software should be chosen to manage analytical control plans?
In the digital age, many software solutions exist to manage analytical control plans. Among the most common are ERP (Enterprise Resource Planning), LIMS (Laboratory Information Management Systems), MES (Manufacturing Execution Systems), ELN (Electronic Laboratory Notebooks), EXCEL of course, and the latest addition, CIKLab.
Overview of software solutions, advantages, and limitations:
Excel: For decades, Microsoft Excel has been the go-to tool for many businesses to manage data, including control plans. Its flexibility, user-friendliness, and capability to produce charts and graphs make it a popular choice. However, Excel has limitations when managing large-scale control plans. File size can become an issue, as can traceability challenges, data security, and integrity. Real-time collaboration and version management can be problematic. Often, complex macros have to be developed because there's always a missing "dimension" to turn it into an automated and functional solution.
- Advantages: Very low cost, flexibility, ease of use, capability to produce charts and graphs.
- Limitations: Handling large data volumes, need for complex macro development, audit trail issues, data security challenges, collaboration, and remote accessibility problems.
Even though Excel is an excellent tool to start structuring plans, rapidly growing companies that quickly accumulate large amounts of data or have more complex needs soon require more robust and specialized solutions.
ERP (Enterprise Resource Planning): These integrated systems manage a company's entire processes by incorporating various management functions, including quality. While ERPs offer a holistic view of the company and facilitate traceability, they can sometimes lack specificity for the detailed management of analytical control plans, especially analytical subcontracting.
- Advantages: Holistic company view, integration of various management functions, facilitates traceability, inventory management linked to results.
- Limitations: High cost (bordering on astronomical), may lack specifics for detailed management of analytical control plans and analytical subcontracting, complexity, and implementation timeline. Organization-wide project.
LIMS (Laboratory Information Management Systems): Specifically designed for laboratories, LIMS centralize data and manage a laboratory's samples, tests, and resources. While they are incredibly efficient for managing internal laboratory analyses, handling subcontracting and product-specific planning can be more challenging.
- Advantages: Data centralization, powerful traceability management for samples, analyses, and reports, specifically designed for analytical laboratories.
- Limitations: High/moderate cost, challenges in managing external analyses, product-based planning, and control frequencies.
MES (Manufacturing Execution Systems): These systems focus on real-time production management and tracking. They excel at ensuring compliance and traceability on the production line. However, their scope is primarily limited to production, and they may not delve deeply into the analytical aspects of quality control and more complex laboratory analyses (both internal and external).
- Advantages: Real-time production tracking, ensures compliance and traceability on the production line.
- Limitations: Moderate to high cost, scope mainly limited to production, doesn't cover analytical aspects of quality control in detail, lacks subcontracting management.
ELN (Electronic Laboratory Notebooks): ELNs are digital lab notebooks replacing traditional paper-based laboratory notebooks. They are perfect for documenting trials and results, especially for R&D departments, but might lack advanced features for comprehensive quality control plan management.
- Advantages: Moderate to low cost, digital transformation of lab notebooks, efficient trial and result documentation.
- Limitations: Lacks advanced features for comprehensive control plan management, periodicities, and analytical subcontracting.
✨Automate Your Analytical Control Plans with CIKLab.
Each software solution offers specific benefits, but it's essential to consider the full spectrum of needs and the "real pain points" to select the most appropriate tool.
Our solution, available in SaaS, provides a unique platform for managing analytical control plans, automating the administration of:
- Internal and external analyses,
- Outsourced laboratories,
- Specifications,
- Analysis frequencies,
- Results and trends.
CIKLab allows for the integration of control plans with results management, making control planning intuitive, straightforward, and fast.
What are the benefits of CIKLab ?
With low cost, an accessible online solution that requires no installation, CIKLab is specifically designed to meet the needs of managing analytical control plans in the Food sector. The application provides undeniable value when it comes to outsourcing analyses and managing external laboratories.
By using CIKLab on its own or integrating it with other tools, Food Quality Managers can benefit from the optimal approach to comprehensive and efficient management of analytical control plans.
