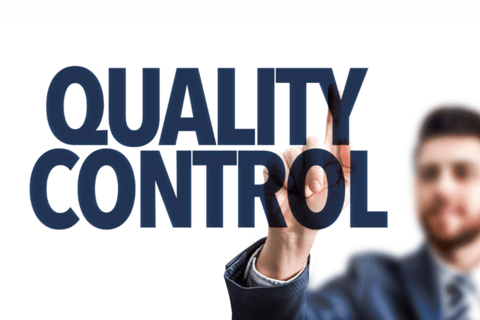
Mastering the regulatory environment
The first step of the Quality waltz consists in knowing the market and the regulatory environment in which you evolve.
For the food industry, it is the EC 178/2002 regulation that prevails. This one stipulates among other things: “a food business operator is best placed to develop a safe food supply system and to ensure that the food it supplies is safe. Therefore, the primary legal responsibility for ensuring the safety of food should rest with him”.
It is this set of regulations that will indicate the standards to be respected on your products, the analyses to be carried out and the expected specifications. This regulatory study is a fundamental step to build the next step; it is the foundation of your entire quality control system. For food supplements, the Synadiet, for example, regularly offers training on the regulatory panorama specific to food supplements. From the regulatory environment, we can categorize the controls to be performed:
- Those that apply to all your products.
- Those that are specific to certain categories of products.
- Finally, the specific controls
Elaborate the control plans
The regulatory analysis allows you to determine the internal specifications that you can apply to your raw materials, production intermediates and finished products, depending on the case.
It is then necessary to adjust the control periodicity. Indeed, the regulation requires an obligation of result. However, it is up to the manufacturer to define and justify the means to be implemented. It is therefore not necessary to systematically test all the parameters of each product. On the contrary, it may be sufficient and interesting to carry out a multiple risk study for each analysis of each product.
Consumer risk and sanitary control
The consumer risk is the most critical. It concerns all risks that have a direct impact on food safety and consumer health. The issue is fundamental and should not be minimized. It can also be about risks that have a high probability of occurring. It is therefore logical to check regularly: microbiological contamination, heavy metals, ethylene oxide, etc.
Then, the company will evaluate the business risk to prioritize the implementation of control plans. What is my exposure to this product or this supplier? What would be the impact on the company of non-compliance and recall of these products or ingredients?
Controlling suppliers to reduce testing
Supplier risk is the one that potentially has the greatest impact on the annual analytical budget. This requires rigorous selection and qualification of suppliers. By ensuring that all quality procedures are in place upstream, the downstream risk is controlled as much as possible. The objective is to rely as much as possible on your suppliers while performing punctual analyses. An ISO-certified, audited supplier who sends you his own control plans and analysis certificates reduces his risk of non-conformity. Their quality rating increases and you can reduce the frequency of tests.
Know your products and adjust your control plans
The product risk is more diffuse. By relying on RASFF alerts or EFSA information, we can know which materials are sensitive or at risk. It will then be necessary to be more vigilant. On the other hand, those that do not pose a problem may have a lighter control plan. It is also the expertise of the company that comes into play and the valuation of its analytical assets. Indeed, each analysis report or certificate sent by a supplier enriches a considerable database that the industrialist can exploit. It is an indispensable resource for monitoring the volatility and risk of a given parameter. Thus, each compliant or non-compliant result has an impact on the future batches to be analyzed. It will also be necessary to pass on this result, both directly to the product, but also to the supplier, and even potentially to an entire category.
With this risk matrix, we will be able to assign a score to each product and each analysis in order to adjust the control periodicity. The critical analyses, having a potential impact on the consumer will be systematic, the analyses having limited consequences for the company will be carried out mainly once at the validation of the material. Between the 2, the frequency of analysis can vary according to the number of batch or a period.
The second step of the Quality waltz consists in establishing the specification sheets, controlling the products and recording the results.
Plan – Do – Check – Act
As soon as you carry out an analysis, you check your products and also evaluate your partners. Every result that is consistent and in line with your suppliers’ results strengthens your confidence and knowledge. When the results are in line, your risk is reduced. This allows you to space out certain controls. Instead of testing entire analysis frameworks, you can rotate through several sentinel analyses. In turn, you can run only a portion of the tests. With your test history, if your result is consistent with your supplier’s, you will have a good guarantee of overall product compliance. Moreover, over a given period, you will have controlled all the parameters. You can also operate on the principle of random control. Each result that is in line with that of your suppliers supports the relevance of your controls and your frequency. On the other hand, each significant deviation should raise questions.
Thus, by knowing your products, your materials and your suppliers, by constantly evaluating them, you can build and update your periodic control plan. This allows you to permanently guarantee the sanitary safety of your consumers and to optimize your analytical budget while minimizing the impact on the profitability of your company.
A tool to control them all (your control plans)
The third step of the Quality waltz is to find the tool to set up your control plans and monitor your analyses and adjust your periodicity.
At the beginning, several Excel files and a precise folder tree are sufficient to evaluate your suppliers and raw materials. However, as your product portfolio grows, or if you want to record and evaluate all the analysis results, you risk losing time with complex formulas and macros. Worse, a quality system with spreadsheets can quickly become a house of cards (ed. note: thanks F-K).
Several solutions have been developped over time to manage quality control in the food industry : ERP, LIMS, PLM. They all have their pro's and con's. A tool like CIKLab, dedicated to the organization of control plans and the follow-up of analyses, from the order to the results, will probably be useful to you.
Check our dedicated article for more information (What is the best solution to manage quality control in the food industry in 2024? )